At a time where the focus of rotorcraft development is on the military, Paul Kennard provides an overview of new technologies being developed by Airbus for the civil helicopter market under its RACER (Rapid And Cost Effective) Rotorcraft program.
It is sometimes easy to forget that other advanced, high speed, vertical lift projects are underway when the headlines are seemingly dominated by the US Army’s ambitious, and expensive, attempt to modernise its helicopter fleet through the Future Long Range Assault Aircraft (FLRAA) and Future Attack and Reconnaissance Aircraft (FARA) programs. Outside of the military, the beautiful Leonardo AW609 continues its ground-breaking progress towards civil certification, both in terms of the air vehicle and Flight Crew Licensing / training. FLRAA, FARA and the AW609 all exploit novel technologies to push the limits of vertical lift.
Current Projects
The FLRAA contenders are a case in point; the Bell V-280 Valor is a developed tiltrotor, leveraging off lessons learned in the development and fielding of the V-22 Osprey, whilst the joint Sikorsky/Boeing SB>1 Defiant is the latest design in Sikorsky’s long line of experimental aircraft to exploit technology showcased on their ‘X2’ demonstrator (which, in itself, was developed from the S-69 Advancing Blade Concept demonstrator of the 1970s). Unlike a tiltrotor, X2 technology retains the main rotor in a fixed plane but stacks two systems coaxially; spinning in opposite directions they provide the requisite anti-torque control for stability and slow speed handling. The Defiant uses a tail mounted propulsor to provide ‘thrust compounding’ to increase acceleration / deceleration and forward airspeed.
The Sikorsky FARA proposal, the Raider X, is effectively a ‘middle ground’ aircraft. It is very similar to the S-97 Raider scout concept, albeit enlarged, and resembles a scaled-down SB>1 – exploiting the same X2 design features. Bell’s FARA contender, the 360 ‘Invictus’ looks conventional by comparison – a traditional helicopter design with some ‘tweaks’ and a lift compounding wing to offload the main rotor in the cruise. The FARA threshold speed requirement is a far more modest 180kts – a speed that the non-compounded RAH-66 Comanche achieved – so Bell has focused on the lowest risk, challenging Sikorsky to make the X2 Technology work in a production helicopter.
The AW609 is, of course, a tiltrotor. Born as a joint project with Bell (along with the AW139), the AW609 has experienced an extended journey from concept to service. First flown as long ago as 2003, the -609 has had to weather uncertain global market conditions (the Financial Crash and the current COVID-19 providing two significant headwind components), uncertainty from the regulators how to certify the aircraft (leading to a new ‘Powered Lift’ specification being developed) and the inevitable investigations post a fatal crash during testing in 2015. Initially, in 2003, FAA certification was expected in the 2007/8 timeframe; it was predicted that 2020 would, finally, be the year that a civil certification was signed off, but, yet again, external factors are pushing it further to the right.
We have, so far, discussed all the ‘big’ manufacturers and their involvement in advanced vertical lift aircraft – except one, Airbus.
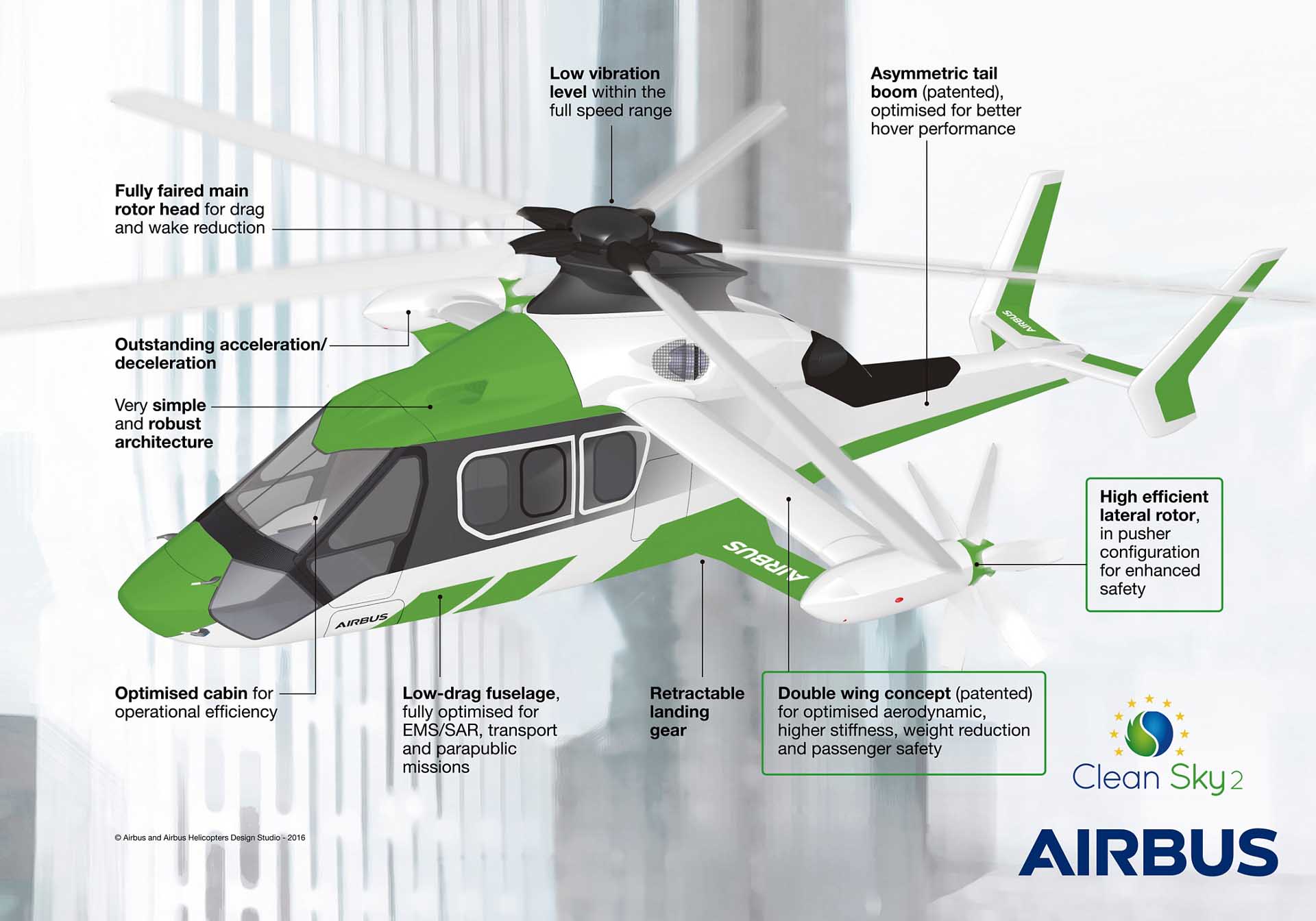
Airbus Direction
Airbus have decided to go in a different direction, eschewing the potential volume of large military contracts (and, doubtless, deciding that neither FLRAA or FARA was realistically going to be awarded to a non-US vendor) and instead looking at a different sector of the civil market; that of high speed, low cost, clean and efficient intra- and inter-urban mobility. The result is the Airbus RACER concept; indeed, the name itself directly references this vision, being an acronym of Rapid And Cost Effective Rotorcraft. The first technology demonstrator is approaching final assembly with a first flight scheduled for 2021. RACER benefits from funding from the EU’s ‘Clean Sky’ initiative, which is investing in Green Rotor Craft (GRC) technologies, such as noise and emissions reductions.
Like the SB>1 and Raider X, the RACER has exploited the outputs from a previous technology demonstration program. The X3 or (‘X-Cubed’) was both innovative and practical at the same time; almost the perfect combination for a demonstration program. The practical part was the use of an AS365 Dauphin fuselage (with the tailrotor removed and replaced by twin vertical stabilisers) and the adoption of the rotor system from the EC155.
The innovation came both internally and externally. The most obvious, external, feature was the biplane lift compounded wing and pair of tractor propellers. This hybrid system combined lift and thrust compounding techniques to permit both the offloading of the main rotor and greater propulsive thrust in level flight. The internal work featured flight control systems to permit differential thrust to be supplied by the propellers to counter the torque of the main rotor, acting in lieu of a tail rotor, and the ability to slow the main rotor in forward flight. This slowed rotor enabled the X3 to achieve a significantly faster forward speed than a regular AS365 by delaying the onset of critical Mach number (MCRIT) on the advancing rotor blade and reducing the required angle of attack on the retreating blade, thereby increasing the forward speed possible before entering the Retreating Blade Stall zone. During its test program, the X3 undoubtedly showed that the essential concept behind the RACER was sound. It was able to demonstrate level speeds in excess of 255kts, climb at over 5000fpm and fly at over 120 degrees Angle of Bank. From a pilot’s perspective, that sounds like a lot of fun!
The X-Cubed and RACER both left me wanting to know more. Luckily, Heli Ops were able to arrange a mutually convenient time for me to talk RACER matters with Tomasz Krysinski, VP Research & Innovation at Airbus Helicopters. I had several questions I wanted to pose, and Tomasz was most graceful and forthcoming in providing answers.
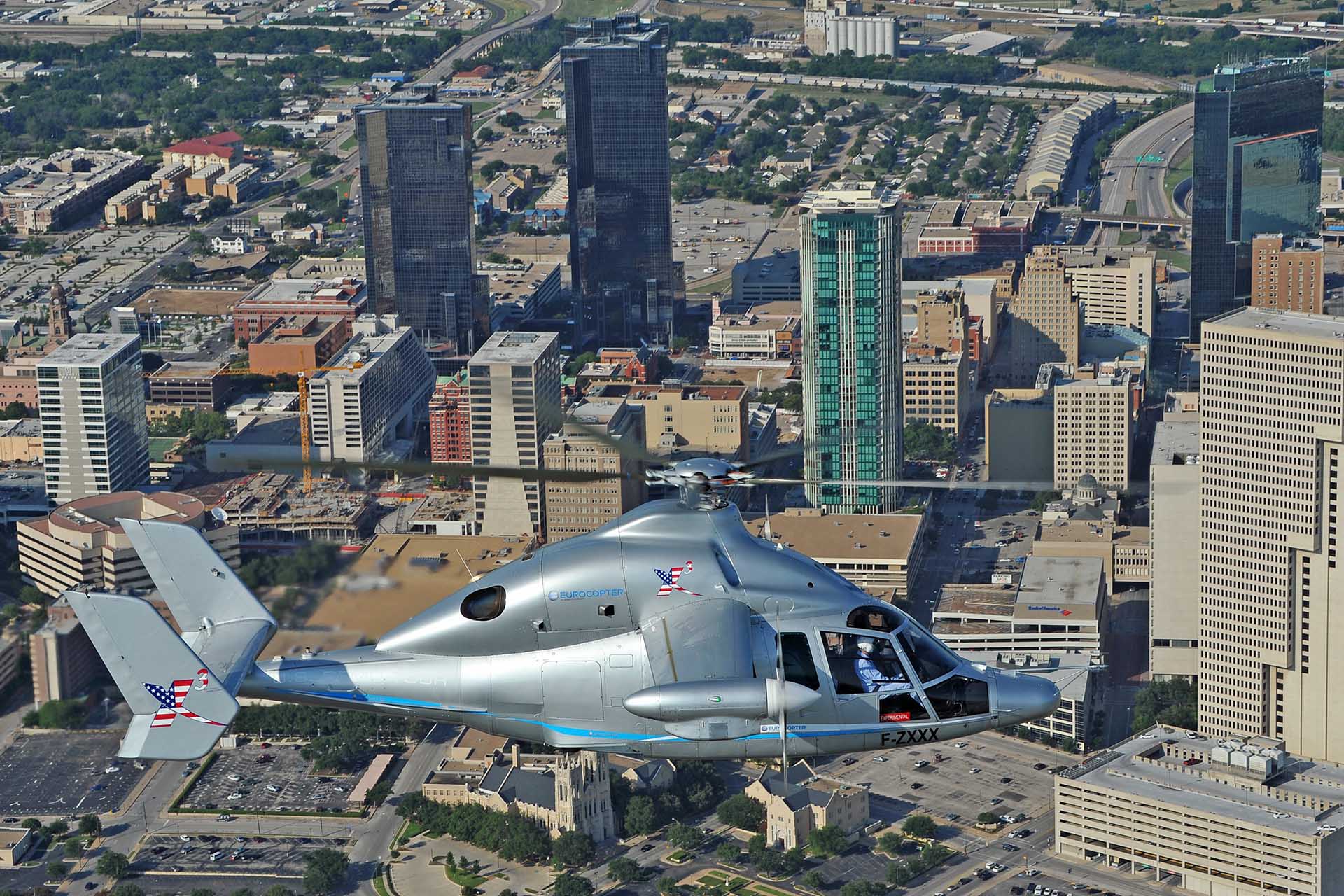
Philosophy
First off the bat, I asked what he considered to be the RACER’s guiding philosophy. His answer was succinct; to be faster, quieter and more economical than a conventional rotorcraft so that it could legitimately expect to be cleared to fly in the congested urban environments of the future. To this end, the RACER must be measurably ‘greener’ and more cost effective than contemporary rotorcraft; in all aspects, including noise, emissions and fuel burn. The estimates for RACER are that it will cruise at 190kts IAS burning 30% less fuel than an equivalent sized helicopter at 130kts. Tomasz went on to note that Airbus’ experience with advanced blade technology will help to reduce the noise footprint of the aircraft; Airbus’ patented ‘Blue Edge’ rotor technology has been flying for several years. Estimates are that in a RACER sized application, new high-speed rotors will reduce the noise generated by some 50% when compared to an equivalent sized helicopter; crucial to winning over increasingly vocal critics of noise pollution in our urban areas. Tomasz also suggested that the aircraft will have a ‘low noise mode’ where the platform will inform the crew when it can trade noise against other factors by reducing rotor speed and/or shutting down an engine.
My next question was why Airbus went for the configuration they did, a hybrid thrust/lift compounded design, but one retaining several recognisable helicopter features?
Tomasz was quick to praise his competitors, noting that the challenge of trying to hover and go fast in the same airframe was never easy. He completely understood the approaches they had taken, but then explained the rationale behind the RACER’s unique configuration.
Airbus wanted to avoid the ‘Convertiplane’ (tilt rotor / tilt wing) as, in their opinion, it added significant weight and complexity to any design. Weight is the enemy of any form of vertical lift, especially one where you will seek civil certification to operate over urban areas, whilst complexity invites the twin issues of cost and developmental/certification risk.
The AW609/V-22 approach is the simplest mechanically but can cause issues with hot jet exhaust damaging surfaces it lands on and air intake for the engine must be carefully managed. The V-280 has a more complex system of gearboxes that enables the engines to stay aligned to the fuselage but tilts the rotors. Both tiltrotor designs have issues with a small disc area by losing hover performance as the strong downwash effectively ‘pushes down’ on the top of the wing – a limitation that the tilt wing overcomes by moving the entire wing. Whilst this greatly simplifies the engine/rotor interaction, and significantly reduces the loss of hover performance due to the wing (the downwash, in effect, is only impeded by the aerodynamically profiled wing leading edge) there is, inevitably, a price to pay; in this case the power required by the wing root motors to tilt the wing, and the increased structural work required to accommodate the aerodynamic and stress loads; in other words ‘you win some, you lose some’.
Airbus’ approach, as explained by Tomasz, was to keep the main rotor at the conventional size for the platform. This provides a known datum to work from and guarantees the necessary (as per CS27 and CS29 certification) hover performance and controllability for heli-deck and heli-pad operations, whilst avoiding excessive downwash and exploiting high speed rotors to minimise noise. The distinctive ‘Box Wings’ are there to offload the main rotor in forward flight, but are stacked in a triplane configuration as it enables the same amount of lift to be generated by a wing of reduced chord; providing less ‘wetted area’ for the downwash to push down on, at a modest cost of increased drag at high speed. Tomasz went on to explain that whilst the rotor looked conventional, it’s intended use at high speed was novel.
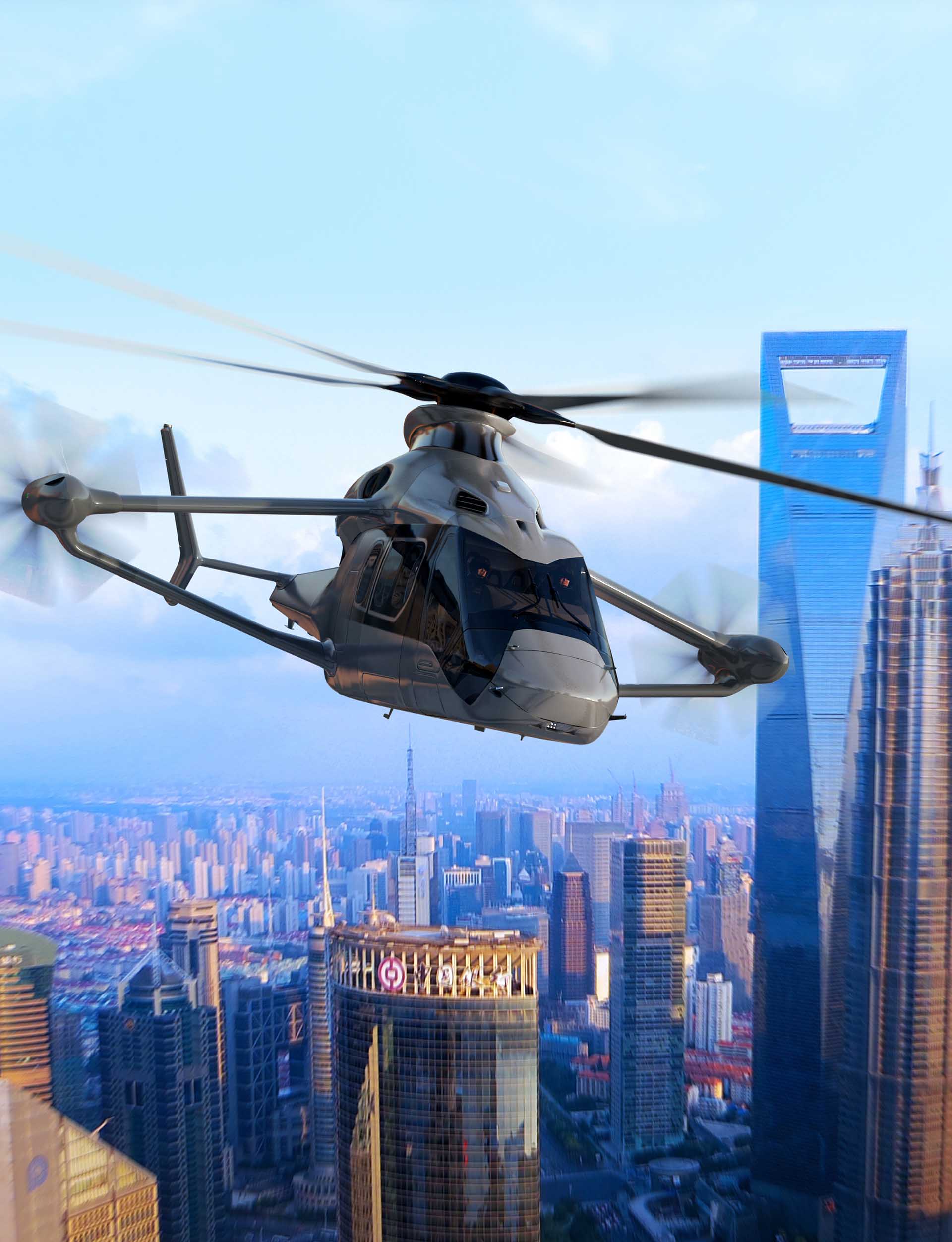
How does RACER work?
Initially, the RACER will accelerate as a normal helicopter. Pitch will be applied collectively to the main rotor, and it will be tilted in the direction of desired travel. As speed builds, the propulsor propellers (changed from the tractor propellers on the X3 for passenger safety and cabin access reasons) shift from a differential pitch mode, providing counter torque in the hover/low speed regimes, to additional forward thrust as the aerodynamically shaped horizontal stabilisers and rear, asymmetric, tail boom offset the torque of the main rotor. Also, as the speed increases, the box wing starts to generate lift. The combination of propeller thrust, and wing lift, enables the rotor to do two things. Firstly, the rotor can slow down (by perhaps as much as 20%) as it’s no longer required to shoulder the entire burden for all the aerodynamic force to keep the aircraft airborne. As explained earlier, this is ‘a good thing’ by delaying compressibility issues on the tip of the advancing blade and blade stall on the retreating side. However, Tomasz added that, at high speed, the angle of attack (alpha) on the advancing blade is also reduced; this creates less drag, noise, component stress and vibration; all key design philosophies for the RACER and contributing to a quiet and smooth cabin experience for passengers. To improve this further, Tomasz stated that Airbus plans to allow operators to routinely shut down an engine once at cruising speed. This will have obvious benefits in terms of fuel consumption (even an engine at Flight Idle requires fuel to overcome the mechanical drag of its components), engine wear and noise.
Whilst shutting down engines has long been a factor in military aviation (Maritime Patrol Aircraft routinely shut down engines to improve on-station loiter time), this is the first time I’ve seen it proposed for a civil certified machine carrying passengers. Tomasz noted that Airbus is working closely with EASA to ensure that routine single engine cruise will be possible. Naturally, both engines will be available for critical flight regimes such as take-off and landing, and, as Tomasz explained, Airbus will fit a significant ‘power bank’ to enable a rapid restart of the second engine in case of emergency; possibly even automatically if the aircraft senses an issue with the operating turbine, similar, perhaps, to ‘stop/start’ technology now routinely fitted to cars. Tomasz also highlighted another advantage of single-engine cruise, namely that, conventionally, engines are scaled for their maximum performance needs being take off, landing and overshoot. Therefore, they are throttled back in the cruise. Whilst this seems sensible, Tomasz suggested that working one turbine harder, perhaps at its ‘sweet spot’ in terms of specific fuel consumption, would also be more fuel efficient than running two engines at cruise setting. The cruise efficiency is further improved by careful aerodynamic streamlining of the fuselage, fitting a retractable undercarriage and some clever Formula One style vortex interactions generated by the Box Wing.
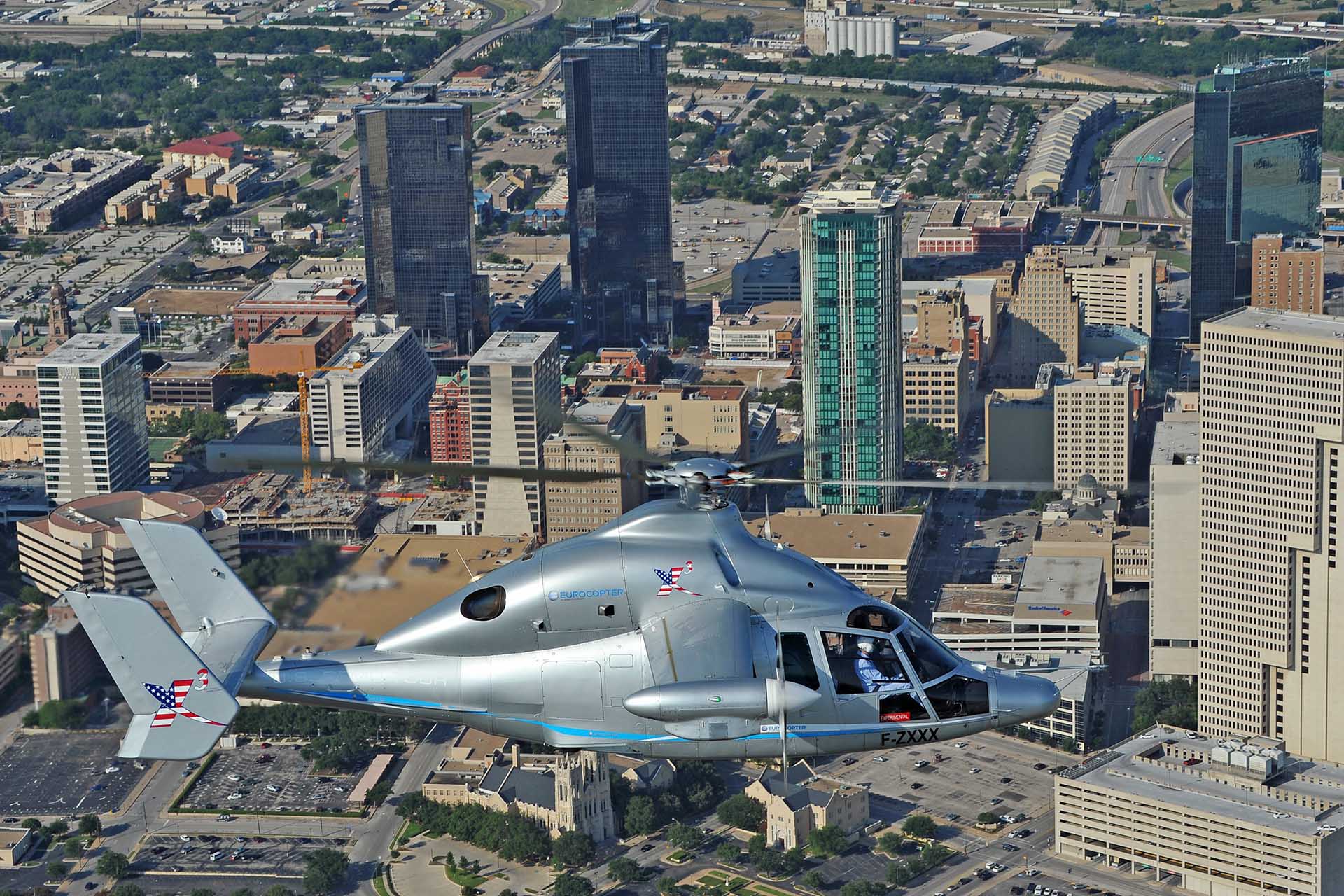
Crew Training and Licensing
As well as investigating how routine One Engine Inoperative (OEI) passenger operations may be conducted safely, EASA also has an interest in and responsibility for Flight Crew Licencing (FCL). Here, again, Tomasz explained the RACER is a simpler proposition for current helicopter operators as there will be minimal re-training for current helicopter pilots. The RACER will fly like a conventional helicopter – just goes faster – so only a short element of conversion training will be required (I look forward to an invitation to find out…!!!) saving time and resource.
This contrasts with tiltrotors; EASA and the FAA are having to develop new qualifications and training routes for ab initio civil tiltrotor pilots; the only current source of qualified pilots is the outflow of V-22 crews from the US Military. The route for a civil tilt rotor pilot is potentially expensive, having to show ability and training in both conventional helicopters and small turboprop fixed wing aircraft. Almost inevitably, the RACER will have growth paths to semi and fully autonomous modes; the former to offload crew workload, whilst the latter offers the opportunity for the airframe to operate as a UAV for certain tasks, perhaps carrying additional cargo, fuel or sensors.
Traffic Awareness
Speaking of sensors, if it is going to operate safely in the urban airspace of the future, the RACER will need to detect hazards and interact fully in the InterCitys Urban Traffic Management (UTM) network of manned and unmanned air vehicles. Tomasz notes that technologies such as those showcased by the Airbus EAGLE (Eye of Autonomous Guidance and Landing Extension) project will inevitably become more important as urban airspace becomes ever more congested. EAGLE is a ‘machine-learning’ system that uses high definition cameras to sense what is expected or selected by the crew (eg a rooftop helideck) then detect ‘strangers’ in the scene, such as a flock of birds, UAV or, perhaps, a change to the surroundings such as a new obstruction in the vicinity using advanced algorithms. The RACER will need such systems to assure safety when the network of electronic conspicuity (ADS-B or similar for UAVs) fails, or there are uncontrolled non-conforming ‘intruders’ on the transit and approach path. Tomasz also notes that a system like EAGLE can also make another few percentage points of economic efficiency, by identifying, selecting and displaying the optimum route/flightpath for the crew, cognisant of other traffic, hazards and weather effects and providing that crucial workload reduction for the crew, allowing them to focus on matters of most importance such as look out and aircraft handling.
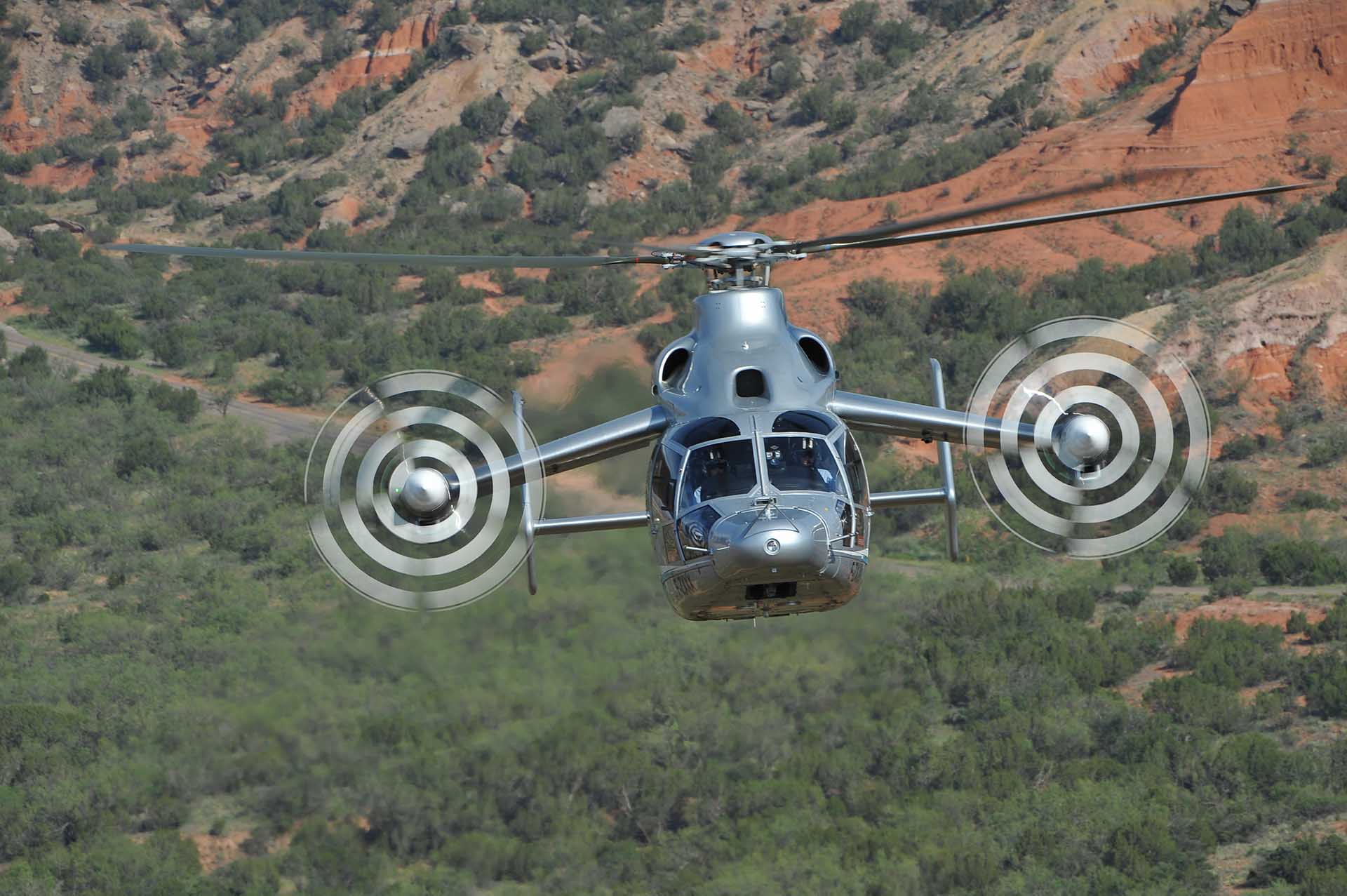
Market View
As stated at the beginning of the article, Airbus have elected not to pursue the US Army’s Joint Vertical Lift projects with RACER. I asked Tomasz where he saw the market, outside the obvious VIP and UTM functions. Immediately he responded with HEMS. He noted the importance of ‘The Golden Hour’ to a casualty’s chances of survival. I can relate to his point having flown MERT missions in both Iraq and Afghanistan, often wishing I could get a few more knots out of the aircraft or reducing the level of vibration to permit delicate procedures to occur safely in the cabin. As Tomasz continued, RACER is both fast and smooth; although optimised for the efficient cruise at 190kts, it has the design potential to exceed 220kts when speed, not fuel burn, is the priority. In time, may well reach the X3’s 250kt+ ‘red line’. Combined with the ability to use most if not all existing HEMS helipads/decks with little to no modification and generous cabin size, RACER, in my personal opinion, looks like a tailormade replacement for the popular H135/H145 in the HEMS role, albeit likely with a side rather than rear loading scheme. Tomasz also noted that the RACER’s combination of abilities make it an ideal SAR machine; the ability to fly quickly to a datum then either hover over the survivor (again the large cabin helps) or, if the need is to conduct a ‘scene of search’ then the RACER can increase its on-station time by shutting down an engine.
Military Application
When asked if he saw a military application for RACER technology Tomasz was, understandably guarded. He allowed that the combination of speed, manoeuvrability and cabin size did lend the RACER to several niche military roles.
In my mind these are Combat SAR, Special Forces support and light utility. The French currently use the H225M (formerly EC725) Caracal for
CSAR. This Cougar-derived aircraft is a capable and well-respected machine, which has achieved a creditable level of export success.
Although one might expect the Caracals to eventually be replaced in the CSAR / SF support role by the H160M, of which the French have
ordered over 160 examples, there must surely be a case for RACER-derived airframes in both roles, and for the even more specialist French
Air Force helicopter air-intercept capability, used to protect key facilities and events from encroachment by light aircraft and UAVs.
Having been a small part of the team that developed the air-air intercept capability for the London Olympics in 2012 I can attest that it’s
not as simple as it sounds, especially if the intercepting helicopter and ‘target’ are broadly comparable in speed. The ‘dash’ speed of the
RACER would make the geometry of such intercepts much more flexible. I’m sure that many countries who traditionally try not to buy US
products will be looking at how RACER develops to see if it will become a viable, non-ITAR, alternative to the winner of the FLRAA
competition.
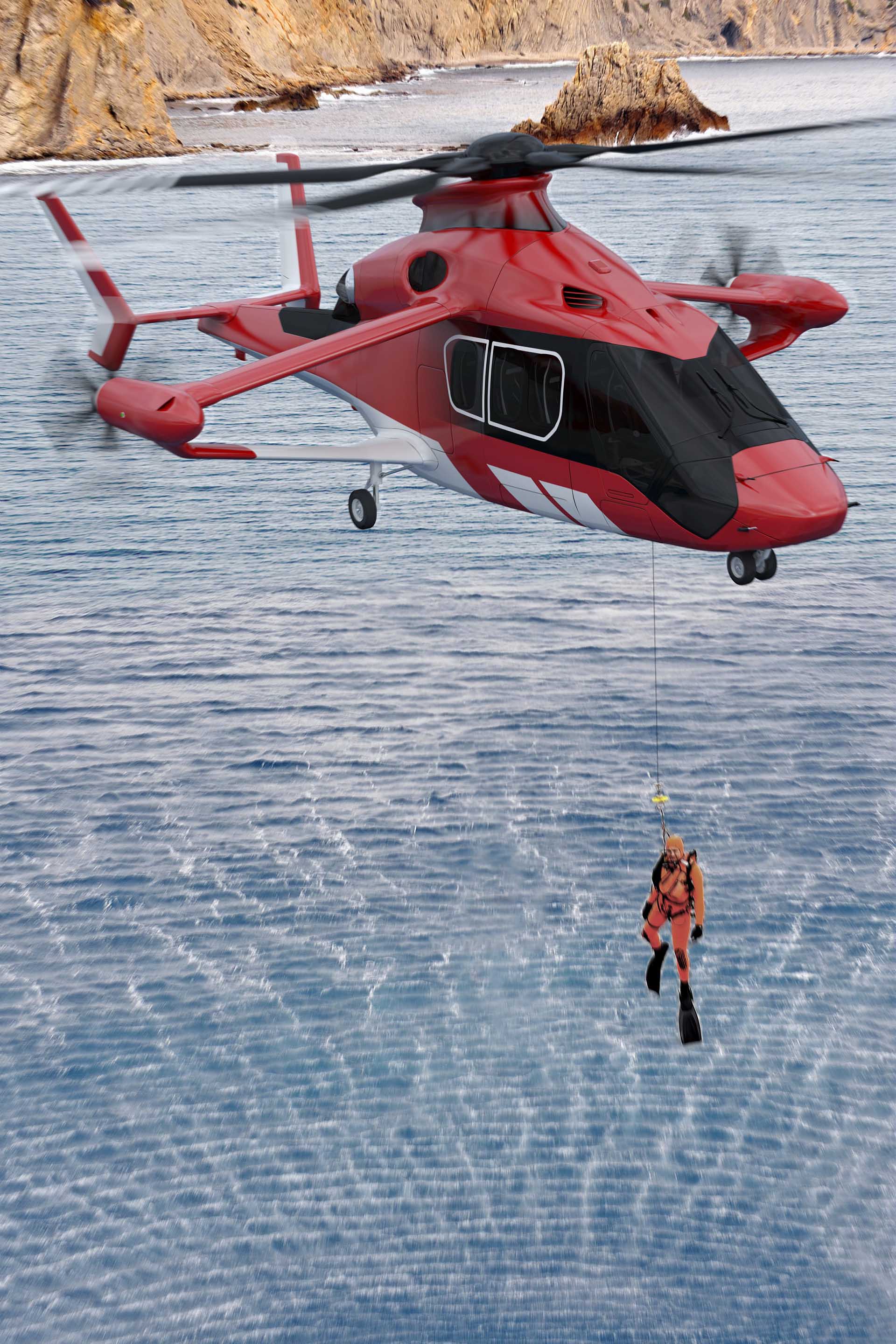
As the prototype RACER enters the home straight towards first flight, I, like many look forward to seeing if it can deliver on its evident
promise. It will also, perhaps, form part of a renaissance in European vertical lift design as it and the Leonardo AW609 take the
next-generation rotorcraft ‘fight’ to their US competitors. I for one can’t wait.
The author is grateful to the generous time that Tomasz Krysinski made available for a Q&A, and to Gloria Illas and Laurence Petiard of
Airbus Helicopters for making the necessary arrangements.