Unlike small single-engine helicopters, which are frequently pilot-only operations, operating larger, more complex machines on precision utility work requires a team of personnel, each with their own specialty and tasks. The on-site crew of a CHI Aviation S61 ‘Shortsky’ flying powerline work in Hawaii discussed their operation with HeliOps’s Ned Dawson.
The Sikorsky S61, although an older design, is still a mainstay of many heavy-lift operations. The big machines can lift around 10,000lbs and Command Pilot Kurt Ventura stressed the importance of tight teamwork when operating such a large machine. “I came from small aircraft where I did pretty much everything on my own, but on a big machine like this you just can’t work like that and that was a bit of a culture shock,” he said, and advised that the usual crew for the S61 on powerline work is four or five people, comprising the pilot, co-pilot, crew chief, fuel truck driver/ground crewman, with an additional ground crewman sometimes if required. “Having good communication is the key. The guys in this group have been doing this a long time and we all bounce everything off each other. As a pilot you really rely on the ground crew because a lot of the time, we can’t even see the ground, so he’s calling everything for me and directing me what to do because he can see stuff that we can’t,” he outlined.
Crew
The ground crew have a wide variety of tasks and responsibilities as they are also A&P mechanics, responsible for the operational condition of the aircraft and equipment. Crew chief Rob Sampson has around eleven years of experience on S61s in locations around the world. He explained that he is also responsible for spotting on the site and coordination with the pilots. Fuel truck driver and ground crewman Milton Kalani has been working around helicopters since 1984 and has been with CHI since 2006. He works from the yard but can also be required on-site if a second spotter is deemed advisable. “The other spotter and fueler have just as dangerous a job in the yard as I have out on-site, and if we need a second spotter on site or at a second location, we’ll use Milt’ for that. During a day you’ll wear forty different hats because there are that many different things that we have to do to get the job done.” stated Sampson. Teamwork within the group is paramount and Sampson remarked that he views everyone as being alongside, left and right of one another rather than senior/junior or over/under each other. Ventura gave the example of a recent lift job. “We had an emergency pull on the east side and the pick-up of the pole was from one site, while the drop site was in another area, so everyone was utilized on the ground. Milt’ (Kalani) was not only fueling but also spotting and calling for us. With the amount of weight we carry, things can go south real quick so everything is pre-planned and controlled. Slow is fast, and nothing can be rushed,” he remarked.
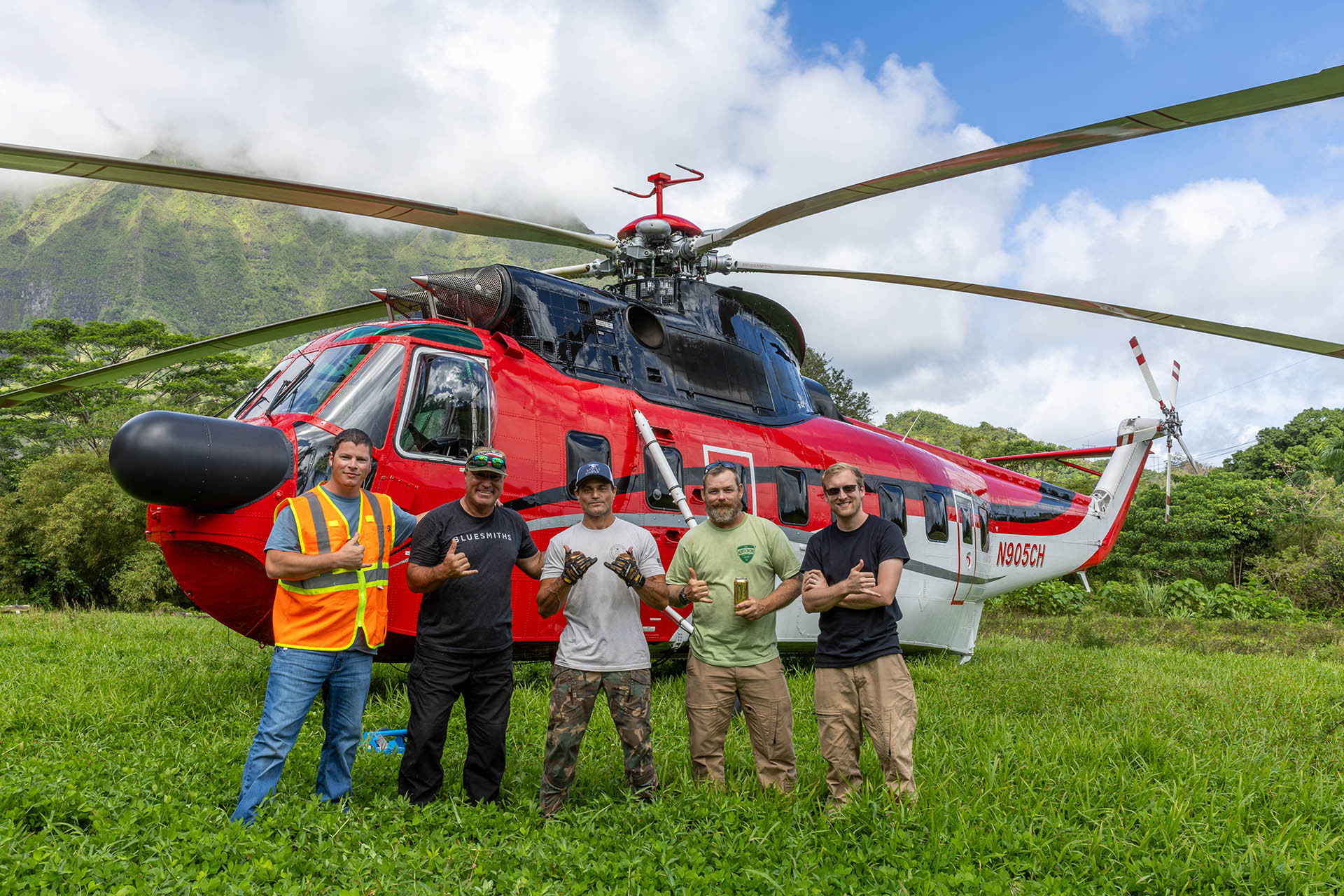
The group works from a portable office/workshop and before the helicopter commences work, Kalani has to drive the fuel tanker to a suitable
position to support the work to be undertaken. This entails checking the roads before going in and can even require an initial trip in a
car to check out roads that may be a little too tight. “We all work together and we’ll check the roads, look at the lines where we’ll be
working and where the poles are, until everyone feels solid about what we’re doing,” he explained. Sampson outlined a typical work routine
for a day of lifting work, explaining, “Usually when we land at the site everyone works together as a group to prep’ our side of the
operation. The hook and line are set out and the pilots work with the maintenance personnel to set everything up.” At that point the
maintenance guys switch hats to be spotters that also know about construction work.
Planning
If possible, Sampson likes the whole crew to then go to the work site and confer with the project ground team there who will be doing the construction work. They establish what work is to be done, how everything is to be rigged and conducted, and in what order, with everything bounced off everyone involved. “We talk to their lead guy running the project to get his plan and if something doesn’t gybe because of the way the helicopter has to do its work, that’s when we’ll start getting into the details. Ninety percent of it will be bounced off the pilots and it’s all based on a lot of experience,” Sampson related, pointing out that just loading the aircraft required careful thought and planning, with tools, equipment and lifting gear loaded in an order that left each item accessible when it was needed throughout the day’s scheduled work.
Once the plan is finalized, the pilots go back to the aircraft and when they advise the ground team that they are ready, the crew chief goes back over the plan and confirms it with the command pilot. “If there’s anything he doesn’t like about it, then we’ll talk it out as a whole group to make sure that everyone is on the same page. That includes the guys in the yard who may be hooking stuff on back there as well,” Sampson elaborated. Before departing from the staging area, aircrew and ground crew talk to each other to check comm’s, and then do the same with the ground crew at the work site to check comm’s there as well. “As soon as I can see or hear them coming, I’ll start talking to them and as soon as we know our comm’s are good, then it’s game time,” he explained. “And on the aircraft heading out there, we’re plugged in on comm’s, out the window with our heads on swivels, because this is a training area and there is always traffic that could fly into us. Once we’re working on the line spotting, there are a multitude of different hazards to watch out for so our heads have to be on swivels there too, while continuously spotting the load, communicating with and directing the pilots.”
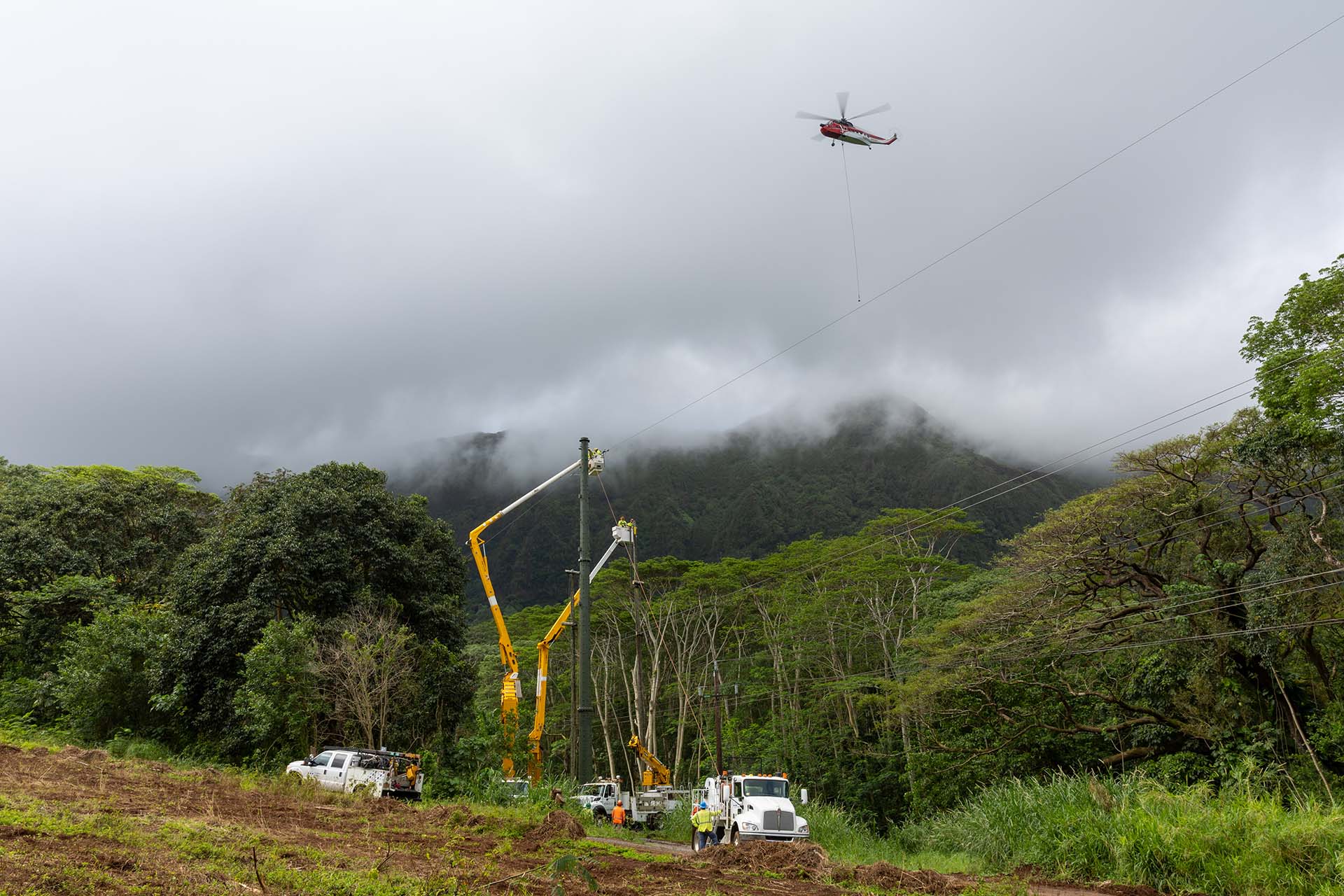
Execution
Once a powerline job starts, there is little or no room for delay or breakdown as the lines are shut down for the work. Shutdowns are to a strict timetable as the rest of the network has to cover the out-of-service section and the increased load can create issues for the network if it goes on too long. “It’s loading up the grid somewhere else so once we start, we have to finish,” noted Ventura. Work planning takes account of this though, as the powerline crews know their work capacity and do not schedule for unrealistic workloads. Appropriate scheduling and the precise planning of the helicopter group has so far ensured that all intended work has been successfully completed within the relevant programmed outage duration.
The work carried out by helicopters on construction is surprisingly varied and a day can involve anything from a single lift taking a few minutes, to a full day of ferrying cement/concrete to a new structure, involving maybe forty or fifty 4,000lb lifts. “That’s a non-stop moving process in the yard, where they might have anything from six to nine trucks bringing in the cement but it’s a long day for the pilots too,” Kalani acknowledged. The buckets of cement have to be flown out to the structure and set lightly on a hopper to be offloaded. The wet cement cannot be dropped more than three feet vertically, otherwise it can start to separate, so the hopper feeds to a pump that then pumps the cement to the destination hole. Wherever possible, longline work is conducted with a 100ft line, as anything shorter creates a downwash problem for personnel and objects underneath the heavy S61, while anything longer poses greater maneuvering challenges and reduces the pilot’s ability to distinguish detail at the ground level. The large machine carries its underbelly hook about six feet behind the pilot, making for a swing issue when pedal-turning; something not encountered with the smaller machines that position the hook almost directly under the pilot.
Accessibility for ground vehicles dictates much of the work that helicopters are required for, so a lot of their busiest workdays are at remote, steep or isolated locations. “Today they only needed us to do one lift of the topmost six-foot vertical section of an old wooden structure that they are replacing with a new steel structure. Because we can lift a lot and it is just as easy for us though, we negotiated with them and ended up pulling down the whole top forty feet in that one lift. That made things a lot easier for the ground construction team, and they were really happy about that,” recounted Sampson. Work on previous days had included setting the new steel structure and transferring the top shielded-fiber wire from the old tower to the new one.
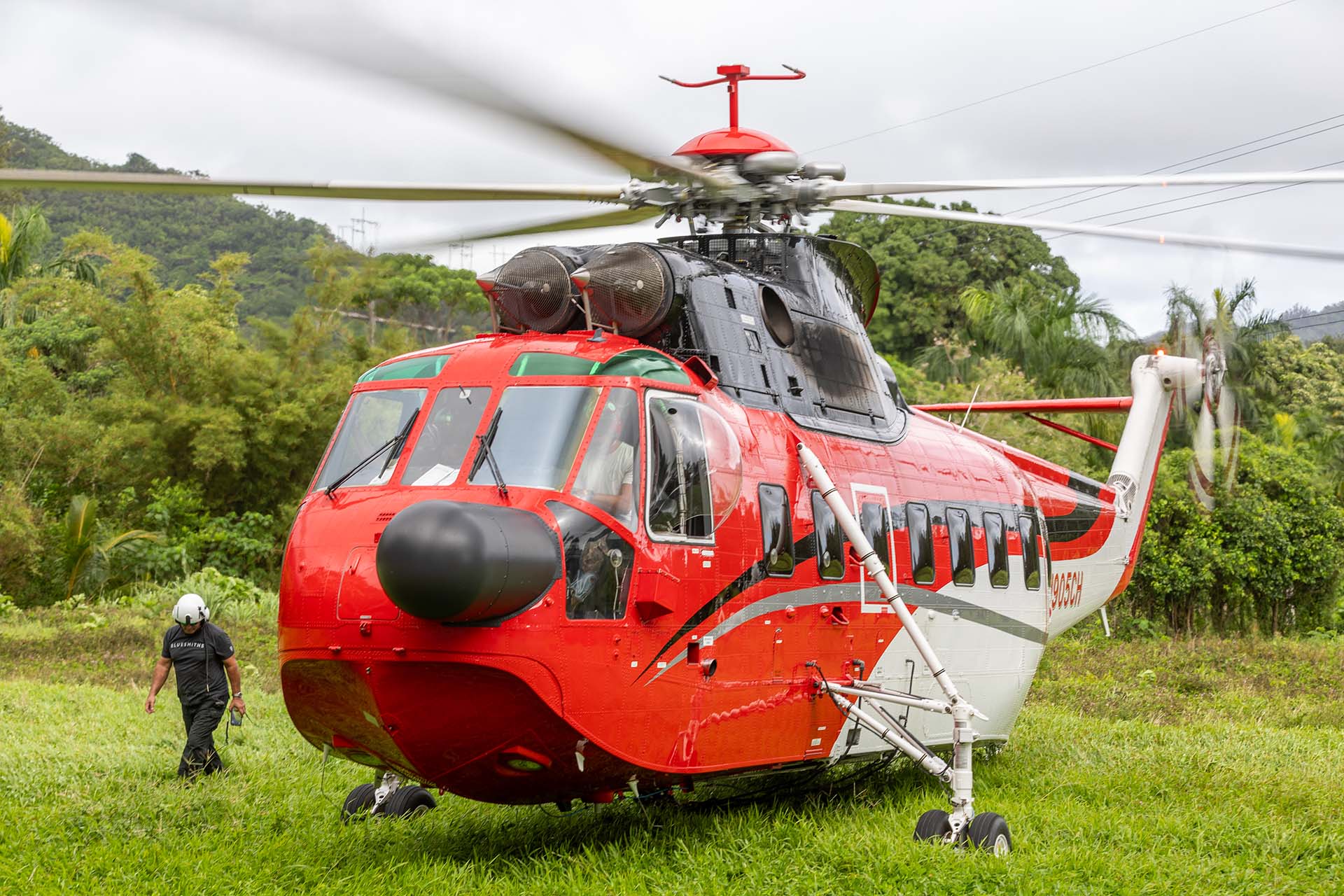
Workhorse
Although the S61 is able to lift far more than is often demanded of it, Ventura opined, “If we can lift it, it’s going to come out.” Kalani added, “Overkill is a good thing. States and counties often want to go for the cheapest option, but I always tell the line guys, it’s nice to have this machine with pretty much all the power in the world to do whatever we need to with it. To me that’s a much safer way of doing stuff.” Safety is key as there is a great deal of risk inherent in the type of work that the CHI crew carries out. “Although there is a lot of risk, we mitigate it by having all these sit-downs, talks and planning sessions, involving everyone. Importantly, if anyone sees anything wrong at any point, they can halt the whole process, shutting it down until we’ve talked about it and found a solution,” said Ventura.
“I’ve been on load transport all around the world, on firefighting with the 61 and on construction for about a year. I’ve been equally responsible on all of them and it’s the best job I’ve ever had,” Sampson enthused. “The huge difference with this is that it’s such precision work. Somebody can put a box into a field, but they aren’t going to be able to put that box into your hand so you can push it left and right by inches and then set it down exactly where it needs to be.” He related that it is not uncommon to have to manually maneuver loads in Hawaii because the powerlines often run through or under heavy forest canopy, and the pilot has only minimal visibility of the ground and crew, with limited options of where to lower the loads. Sampson praises the S61 for its remarkable versatility, with variable configurations that permit a vast range of missions and capabilities.
The newest member of the ground crew is Kyle Loudenbeck, an ex-airline mechanic who left a cargo airline to join CHI in September 2022 and was doing a three-week stint with the S61 in Hawaii. “I needed a change of pace and the base at Howell, Michigan is much closer to where I live,” he cited as reasons for the change. The A&P license covers him for both fixed-wing and rotorcraft, but he acknowledged that it is impossible to jump straight from one discipline to the other and be immediately effective and competent. “The only thing you really need, though, is a willingness to learn, particularly because fixed-wing and helicopters are totally different animals,” he commented. His transition to the rotary-wing environment started with a week of INDOC training, after which he worked on the hangar floor to learn the basics. “Then one Friday afternoon they told me ‘On Monday you’re going to Hawaii for three weeks’, and here I am.”
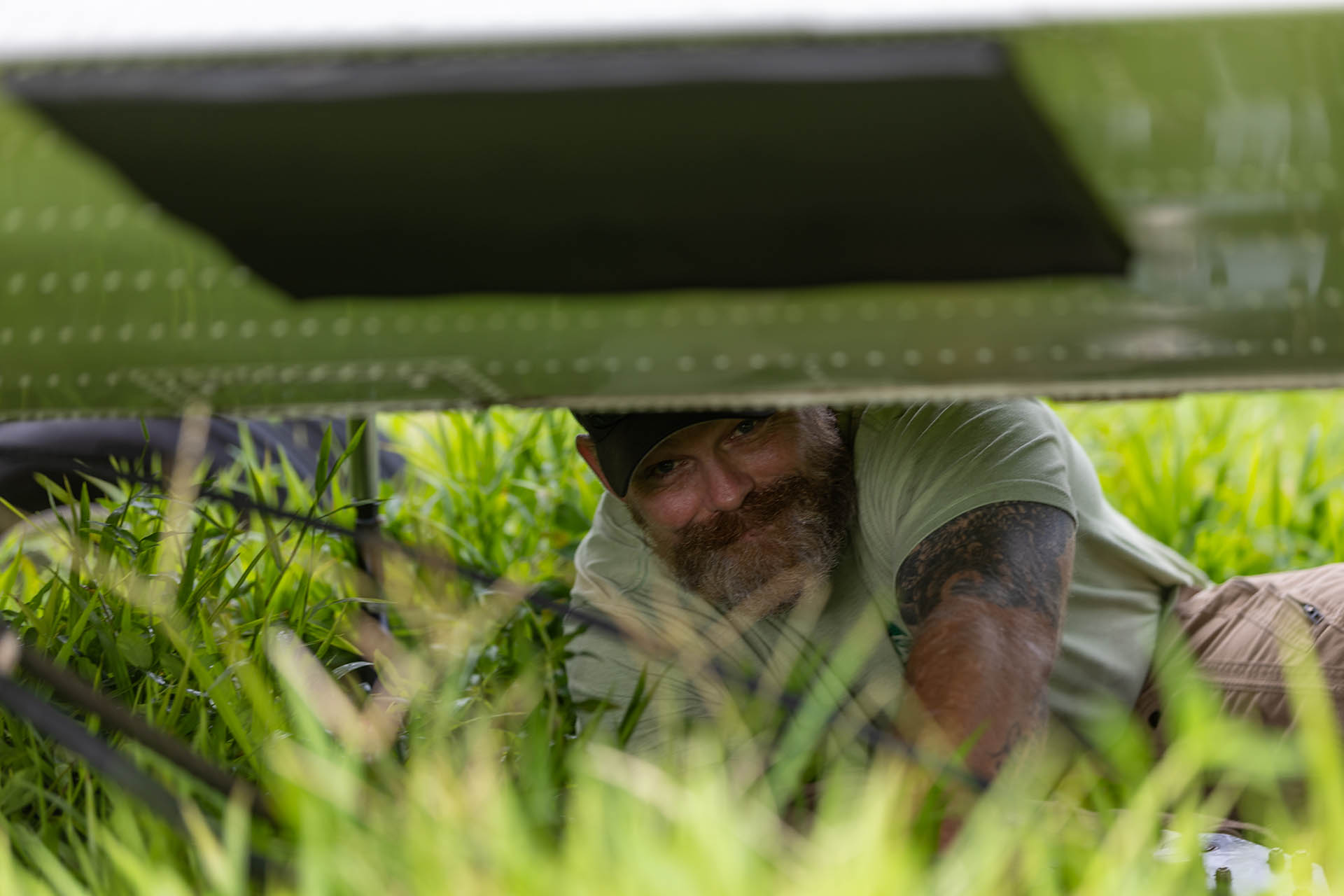
When quizzed about his impressions of the job so far, Loudenbeck remarked, “I really like it. I like to see the world and travel; I enjoy the people I work with and there is a lot to be learned.” He finds the S61 a little easier to work on than the airliners he is used to, as it has non-retractable landing gear and is non-pressurized. I feel comfortable working on it because, as Rob (Sampson) said, if you can read a book, you can work on this aircraft. Where the learning really comes in on this job is the construction side, which is where we wear several hats and that is completely new to me.” Loudenbeck has yet to act as a spotter and Sampson explained that a vast amount of training is involved in getting someone up to speed to even just work around the yard. “That’s where we have Milt’ with almost forty years of experience working around helicopters, doing these kinds of tasks. He provides the oversight of a new guy who is not too familiar with what’s going on, and that experience is the glue that binds the group together,” he commented. “When you’re learning out on the worksite, there’s a comfort level that you have to reach yourself, and also with the pilot and the spotter that’s training you. If you’re not making the grade, then it’s back to the yard for a while until you can come back out and try it again. The final decision is made among the group but predominantly by the pilot. That’s because the rapport, trust level and cohesion that guy has to have with the pilot is huge. He has to know that what you’re calling is correct and be comfortable with the picture you’re painting – the view you’re giving him in his head.”
OJT
On the Job Training (OJT) for spotters is very carefully structured and monitored and Sampson advised that the trainee first observes the experienced spotter complete a lift or two. “We’ll do that and see how he perceives it, then maybe let him call the next one if he’s comfortable. If that goes okay, maybe I’ll step back and let him make the calls all the way from bringing him in to being done with the job. The key to that though, is that you’re just at an arm’s reach away and if you see something differently or going wrong, you can tap him, he knows to stop, and you take over. That is the handover that has to happen, because people make mistakes and we don’t get upset about it, we learn from it,” he related.
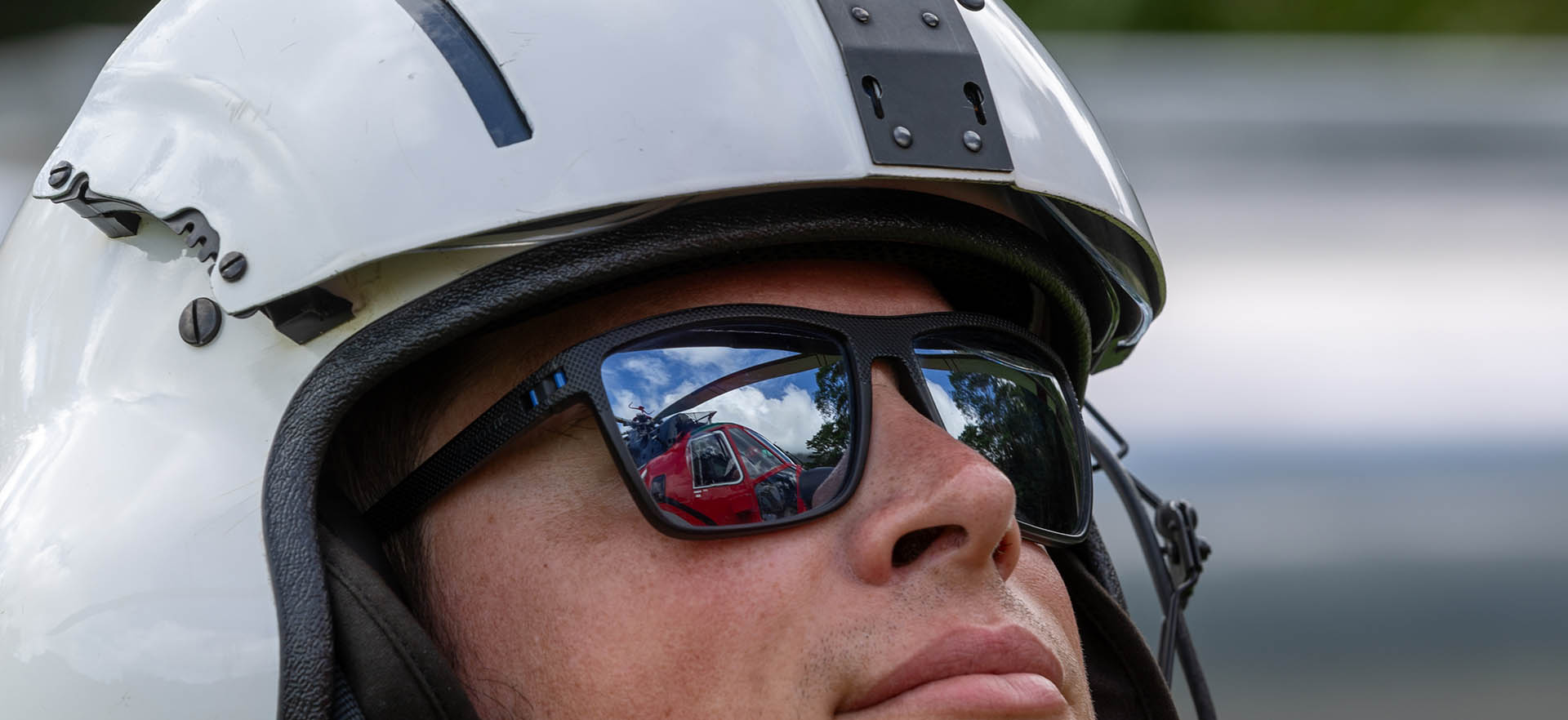
Quality standards throughout CHI are extremely high and this is reflected in the quality of equipment the company uses. According to Kalani, the company owner even requires all the mechanics tools to be of the highest standard, with cheaper or lower quality items expected to be non-existent. Sampson stated that the support team at CHI ensured there were the necessary parts and associated paperwork on hand to maintain the aircraft in operational condition and he reported that he had never encountered any push-back from CHI about ordering extra spares if they were needed. “It’s a never-ending task to stay on top of the parts because there is also all the paperwork that goes with them. As you know, aircraft only fly because there’s a bunch of paperwork done. Aside from that, the hours we fly can build up slowly or really fast, depending on the job we’re working on, so anticipating parts requirements can be a little hit and miss.” Every piece of inventory is electronically recorded on the company computer system, but the aircraft logbooks are all old-school hard copy. “The advantage with this logbook is that I don’t have to do any computer work to take this aircraft, put it on a boat, ship it all the way back to San Diego, build it back up and fly it two or three days back to Michigan. The logbook flies the aircraft, and the computer is for everybody else,” Samson stated.
Co-Pilot Christof Lechner came on board in August 2022, after starting out in tourism and then progressing to oil & gas flying. “I always wanted to fly using a helicopter as a tool,” he stated. “If I’m just flying back and forth, I might as well fly fixed-wings. I’m really happy to be starting out on the big machine because of the integrated crew. In the smaller machines you might work with mechanics, but this is completely different. Everyone has specialties but we work together, and everyone helps out. Drying the line, taking the line in, taking it off, refueling, putting on the blade ties. It’s those small things that glue the team together and out here it’s an amazing, well-oiled machine. I learned a lot every single day and just asked lots of questions. There was no one here that I could not ask any question at any time during those first months. The S61 is an amazing machine and unbelievably nimble for its size,” he opined.
Kalani cited CHI’s top-notch maintenance standards and top-quality equipment as major factors in enticing him to join the company, while Ventura listed some of the aspects he enjoys most about flying the S61 on powerline work. “For me, the powerline industry is the most challenging flying I’ve ever done. I’ve done firefighting and rescue work, which was challenging, but nothing else is as precise as this has to be. Plus, it’s in the big machine and I’ve always wanted to fly the heavies. Like Rob, I also enjoy construction because I love seeing things get built,” he remarked.