Mountain Blade Runner is the brainchild of Bryson Gray and wife Skyla, who started the company when Gray was just 21 years old. The
couple targeted the business at aerial work in mountainous terrain and now, still only in their early thirties, operate a busy fleet of
seven helicopters.
Early Interest
Bryson Gray first became interested in flying helicopters when his father bought an Enstrom 480B in 2006 for the family ranch in Montrose, Colorado. He commenced lessons in 2007, obtaining his private and commercial licenses and then, unlike most new pilots still in their teens, instead of looking for a job as a pilot, he and Skyla – his high-school sweetheart to whom he has now been married for fourteen years – wanted to do something that was secure and didn’t entail moving too far away from home. They decided to start their own helicopter company and immediately began the drawn-out process of gaining approval for a commercial operation.
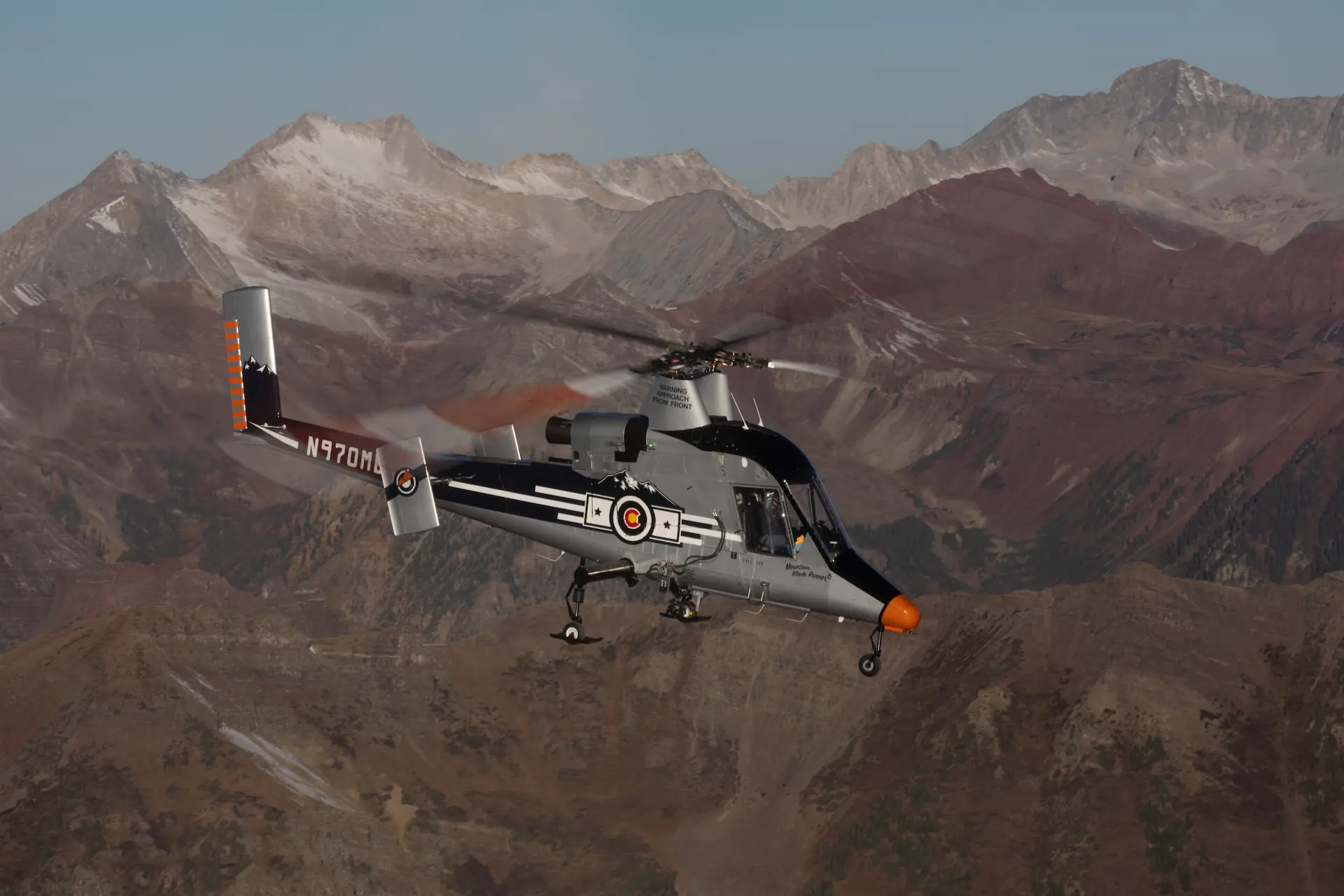
In 2012, Bryson Gray was 21 years old and after two or three years of jumping through the requisite bureaucratic hoops, he achieved Part
135 approval and launched Mountain Blade Runner (MBR Helicopters), very shortly thereafter purchasing the company’s first AS350-B3e (now
Airbus H125). The Enstrom was not suited for the demanding type of operations that Gray intended conducting and he recounted, “I chose the
B3e because of the needs of our local area, particularly the altitudes, and if you’re going to do it, you’ve got to do it right. Our
initial vision was to serve the western US, focusing on work in mountainous terrain.” Normal operations in the local area are from 5,750ft
to over 14,000ft, and landings are commonly made at up to 13,800ft so the hot and high performance of the top-tier A-Star made it the
logical choice for the company’s purposes.
Niche Target
Load-lifting in the typical high-altitude mountainous terrain of the area of operations was the niche that Gray targeted and by the end of the first year of operation, MBR had already become well established in the firefighting arena, initially working on a call-when-needed (CWN) basis and flying between 50 and 60 hours on firefighting missions. A solid base of established business and confidence in future growth led Gray to purchase another B3e a couple of years later and this became an established pattern over the years, with a new machine added to the fleet approximately every two years. By 2022, the MBR fleet had grown to include four AS350-B3e A-Stars, two Kaman K-Max 1200s and the original Enstrom 480B bought by Gray’s father. While the B3e is a highly capable machine ‘out of the box’, MBR has installed the FastFin system from BLR Aerospace - fitted to all four A-Stars; a modification that noticeably improves HOGE (hover out of ground effect) stability, available right tail-rotor authority, and lift capacity. The oldest A-Star is the original 2012 aircraft and the newest is a 2020 example that was delivered in 2021. The 2012 machine still only has around 3,200hrs logged, so all are very fresh, low-time, late model airframes.
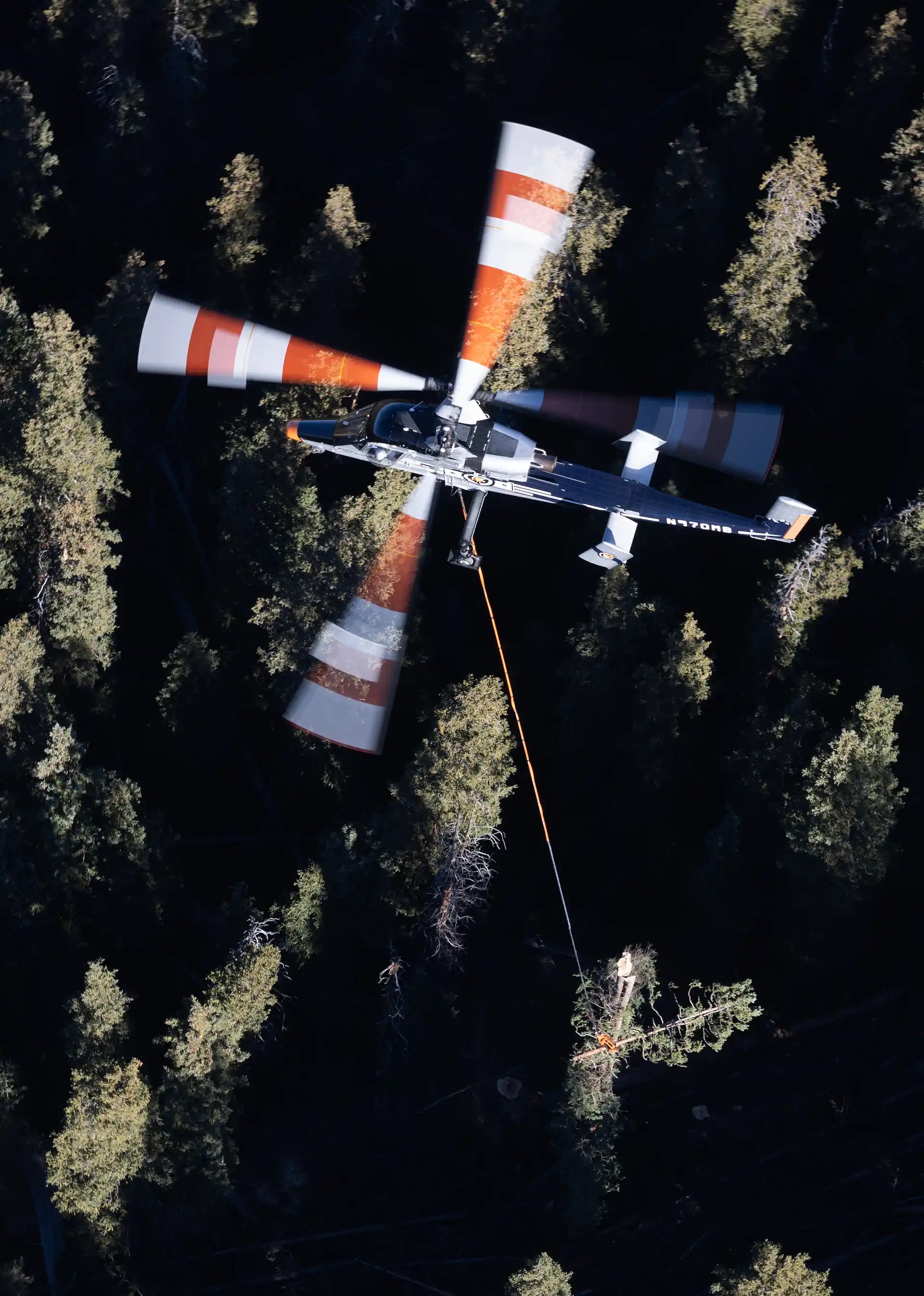
After the initial CWN firefighting work in the early years, MBR’s expanded fleet started to obtain some exclusive use contracts and Gray advised that there is now a healthy mix of exclusive use and CWN work for all four A-Stars, along with the regular demand for the heavier hitting K-Max. Although the business is still headquartered on the family ranch, a large proportion of the fleet is away from base, on firefighting operations for much of May-November, while a small contingent remaining on base deals with any local work.
The nature of the local terrain means that there are always wires around but most powerlines are marked and do not present anywhere near the threat that unmarked mining cables do, and those can be found up to 300ft in valleys. “There are just a few, but they are really scary hazards,” Gray commented.
Right People, Right Equipment
Gray recognized right from the start that to run the type of operation he envisaged, he needed to hire the right people, rather than trying to do it himself as a low-time pilot, and MBR now employs twelve high-time pilots. “Everything we do demands a high level of specific skills. There’s the precision flying that all our missions demand and the altitudes we operate at,” he related. “We like the small company ‘feel’ internally and want to maintain a good life-work balance, not just for us but also for all our employees. Most of our employees are long-term, for a minimum of around six to seven years and several have been with us nine to ten years, almost as long as the company has existed. We’ve got a really good crew and we want to take care of them.”
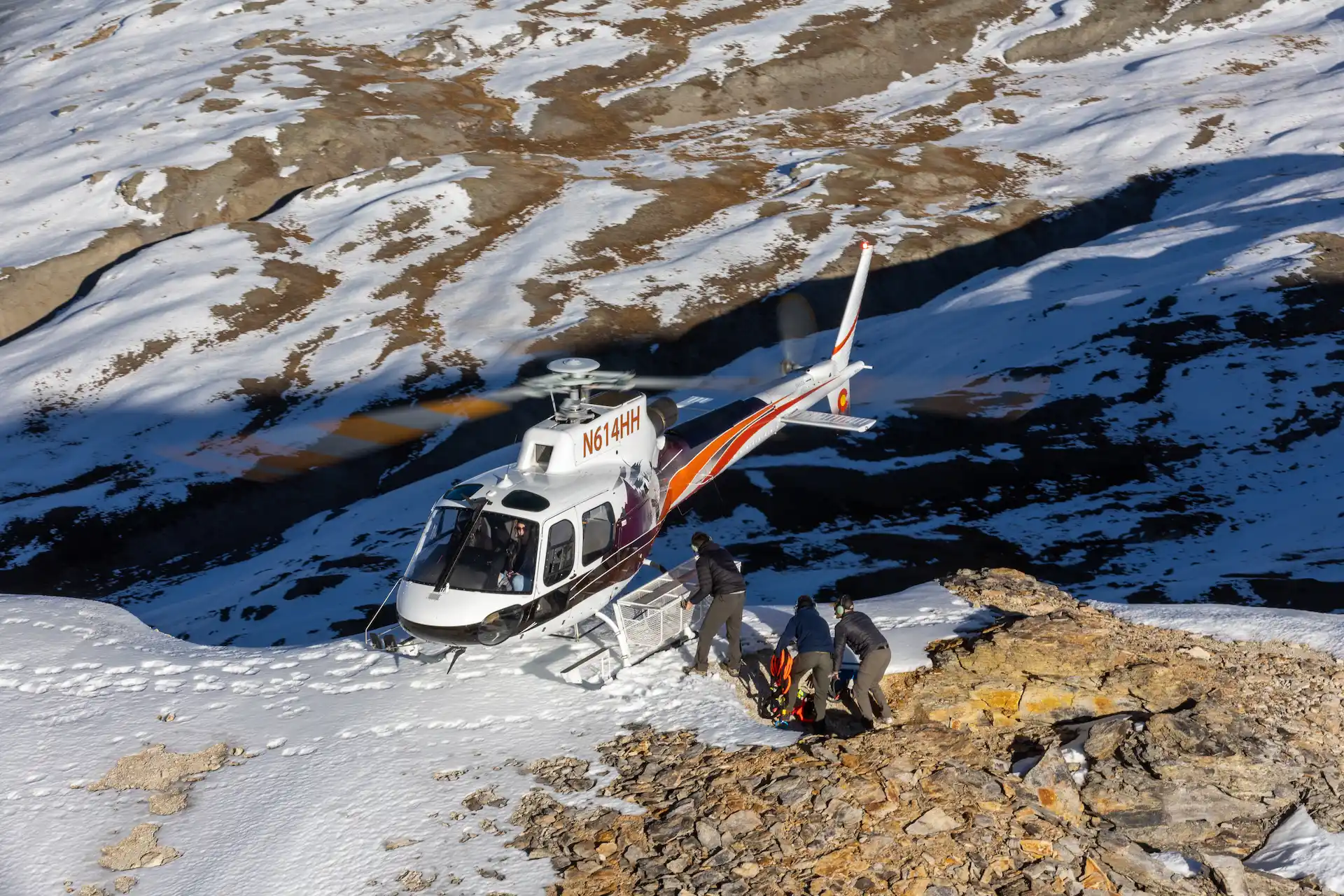
The external load limit of the A-Stars restricted the amount of heavier lifting jobs the company could service, so in early 2019 the first K-Max was bought for its much greater lifting capacity, with a second example joining the fleet around two years later. The only helicopter type in the world to be purpose built for load-lifting, the unusually configured and comparatively noise-friendly K-Max features two side-by-side, outward-tilted contra-rotating main rotor heads, eliminating the conventional tail rotor. MBR’s K-Maxes typically operate up to 12,000ft and the type’s lift performance drop-off with altitude is minimal. Alongside the helicopter operation, the company also runs ground-based logging operations, and the K-Max is an ideal platform for timber recovery, lifting logs up to 4,300lbs. The total K-Max workload is now around 400 hours annually and about half of that is on timber recovery, with the remainder split more or less evenly between construction jobs and firefighting. According to Gray, the primary motivation for acquiring the second K-Max was so the company could pursue further expansion into varied private sector lift-work, while ensuring they could sustain the Forest Service firefighting work.
Flying the K-Max
Pilot Jeff Powers has just over 1,800 hours in the K-1200 with several operators and he described flying the unusually configured machine as more like driving than flying a typical helicopter. “It definitely has a few idiosyncrasies and there are little tricks to flying it that you learn over time that make it much easier. What I like most about it is that you work in a small crew and have no passengers. You’re kind of a one-trick pony and you have a specific job so you just go and get it done.” Depending on fuel load, the K-Max will lift logs up to 4,300lbs at typical operational altitudes and boasts a maximum external load limit of 6,000lbs – more than the aircraft’s empty weight. Powers explained that when loaded, the aircraft is very stable but that at light weights and low power settings – such as on the dip during firefighting operations – it can be a little directionally unstable, particularly in light and variable winds. “I think it’s because then you have two rotor discs generating slightly different lift, but as soon as you load up and put the power on, it immediately settles down and stabilizes,” he elaborated but noted that this handling idiosyncrasy is only disconcerting when new to the type, and quickly becomes a known, manageable handling trait as experience builds.

Powers acknowledged that the K-Max is a type that can bite hard if a pilot is not on top of it however, commenting, “You can’t be slack on the controls, you have to be on top of it and ahead of the game the whole time. Cross-controlling can really get you in trouble as you can have a hub-to-blade strike and without a tail rotor it really weather-vanes.” He explained that due to the weather-vaning tendency, experienced pilots normally operate the aircraft into wind whenever practical, making the flight more stable, minimizing control inputs, and reducing pilot workload. “All in all, though, it’s a dream to operate on longlining. You don’t have to crane over far to look out either side of the aircraft.” He admits that he loves flying the A-Star, as they’re smooth, fast, and comfortable. When it comes to load lifting however, the K-Max is by far his favorite aircraft, and he particularly noted its exceptional visibility. Acknowledging that there are several – possibly apocryphal – accounts of cross-chord blade cracking on K-1200s, Powers makes a point of stopping every two lift cycles to inspect the rotor blades and satisfy himself that everything is in serviceable, undamaged condition but added, “We rely on the mechanics a lot though, because we can operate from 6,000ft up to 13,000ft in a single day and the aircraft flies differently at significantly different altitudes. That means the mechanics have to adjust the rotor flaps to compensate.”
Maintenance
Prior to 2020, mechanic Mike Nelson had worked for MBR part-time alongside his job with another company. When that company closed its doors, Nelson joined MBR full-time and became director of maintenance, now overseeing a roster of ten mechanics who work split shifts to keep the fleet in top shape. Nelson enjoys working from the ranch, away from the airport and petty aviation politics, with the added bonus of exceptional views and abundant wildlife that can include deer, coyotes and even the occasional mountain lion. He cited the diversity in his work with MBR as one of the most enjoyable facets of the job, saying, “It’s not the same thing every day, and even the firefighting seasons are never the same.” Something that was very different for him was the K-Max; a type he had never worked on before. “It’s a very different machine. The engine in it might be zero-time, but it’s a 1956 engine with no FADEC or any technology like that. It does what it does very well, and that’s to operate as a lifting machine.” During the main season when the bulk of the fleet is deployed away from base, Nelson said he hardly ever sees anyone but is kept busy liaising with the pilots, spending time on the phone, obtaining parts, managing the maintenance data and coordinating maintenance needs, and generally ensuring everyone has everything they need.
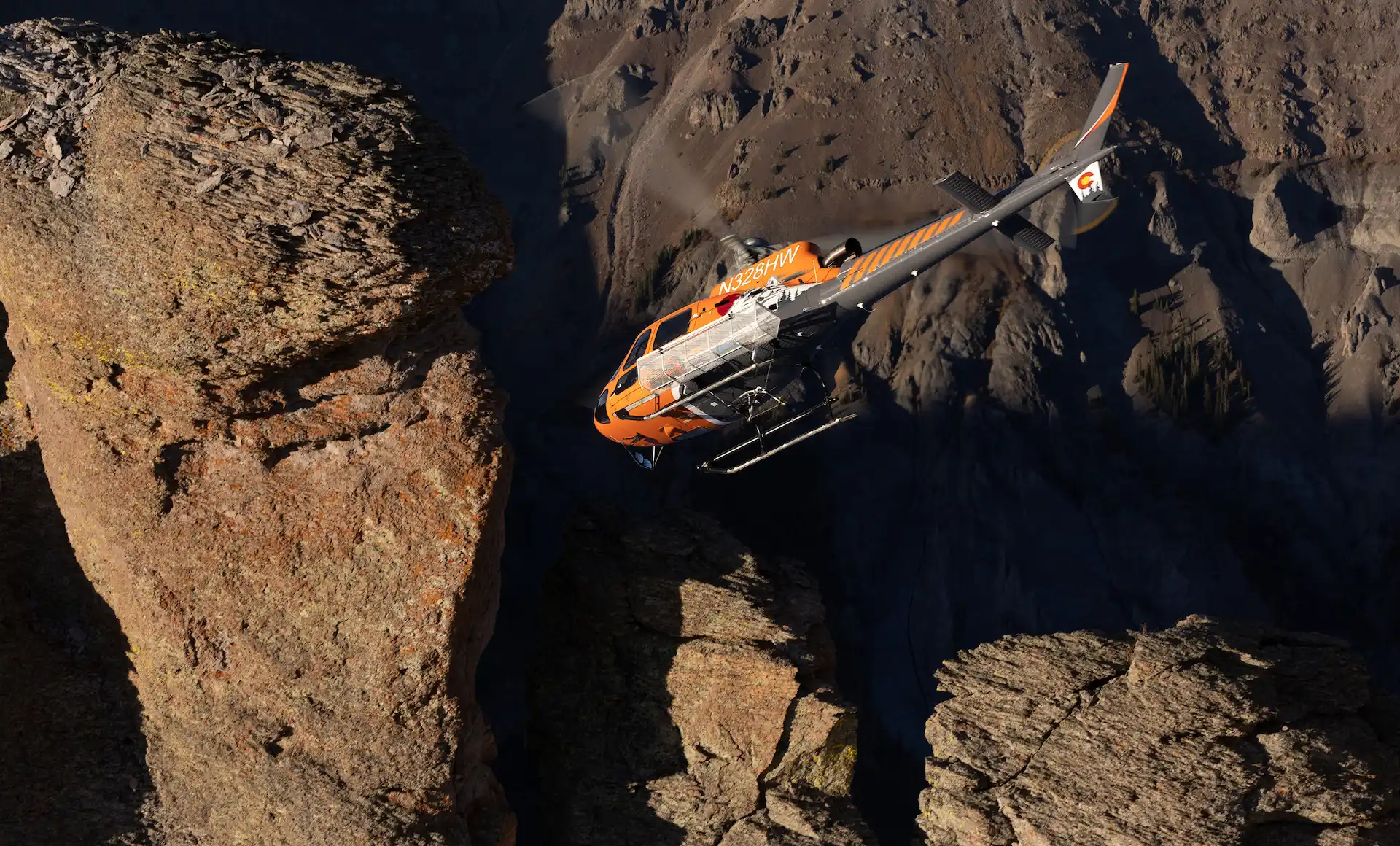
Major 600hr inspections are generally carried out in the winter when the machines are at base, as it is highly problematic to have a machine unavailable for firefighting during the high demand fire season. Calendar inspections and less intensive checks can be done during the season however, either at base or sometimes out in the field. If circumstances dictate though, the skills and capabilities are there to cope with unexpected maintenance challenges. “We did have to do an A-Star engine change out in the field this year though when the 2,700hr engine started making metal on a fire contract in Oregon,” Nelson recalled. “I arrived at 3p.m. and by 4p.m. the next day we had the old engine out, the replacement engine in and had started test runs.” He also acknowledged that it was the only instance he had ever heard of, where an Arriel 2D engine made metal and said that they were known as a particularly reliable powerplant. The defective engine is still being investigated by manufacturer Safran to establish the cause.
Although fleet maintenance is somewhat simplified by having just two primary workhorse types, Nelson advised that parts supply and
technical support can be challenging at times, particularly with the way that Covid devastated the global supply chain. Not only is the
Montrose base somewhat removed from the large centers with ready access to parts support, the MBR aircraft usually operate from remote
locations, so to mitigate the challenges this can cause, every effort is made to keep a stock of commonly required parts on hand. “At least
with the A-Stars, Airbus is a huge company, and many other organizations are also able to supply parts. Tom Brown from Airbus is usually
available and is always really helpful, then if he’s not around we can always call Texas and they’ll help us out,” Nelson stated. “Kaman is
much smaller though and they only built about sixty K-Maxes, with around thirty still operating, so there are far fewer options to find
parts for such a small, specialized fleet. Because they only have two guys to support the worldwide fleet, it means that sometimes you just
have to get in line but if you don’t get hold of Casey, he’ll always call you back.”
Environmental Challenges
Due to the hot and high, dry, high-UV nature of MBR’s operations, Nelson reported that on the B3es, all rubber components were carefully watched for signs of deterioration and tail rotor assemblies closely inspected for wear. “Rubber really doesn’t like those conditions and we work these aircraft hard, lifting heavy loads in demanding environments. With the K-Maxes we’re always looking closely at the blades, although so far, we’ve never experienced a problem with them,” he commented. “The pilots working out in the field are flying in a demanding environment, possibly considering weather, wires, or any number of operational concerns. They’ve got a lot on their plate so if we can, we want to be out there helping them get their aircraft set up just right and make their job a little easier.” Nelson described the K-Max as an ‘awkward’ aircraft to work on compared to the B3e but said that most of the mechanics were trained on both types. “The A-Star is easier to work on in most respects but once you’ve spent enough time working on the K-Max you do get used it.”
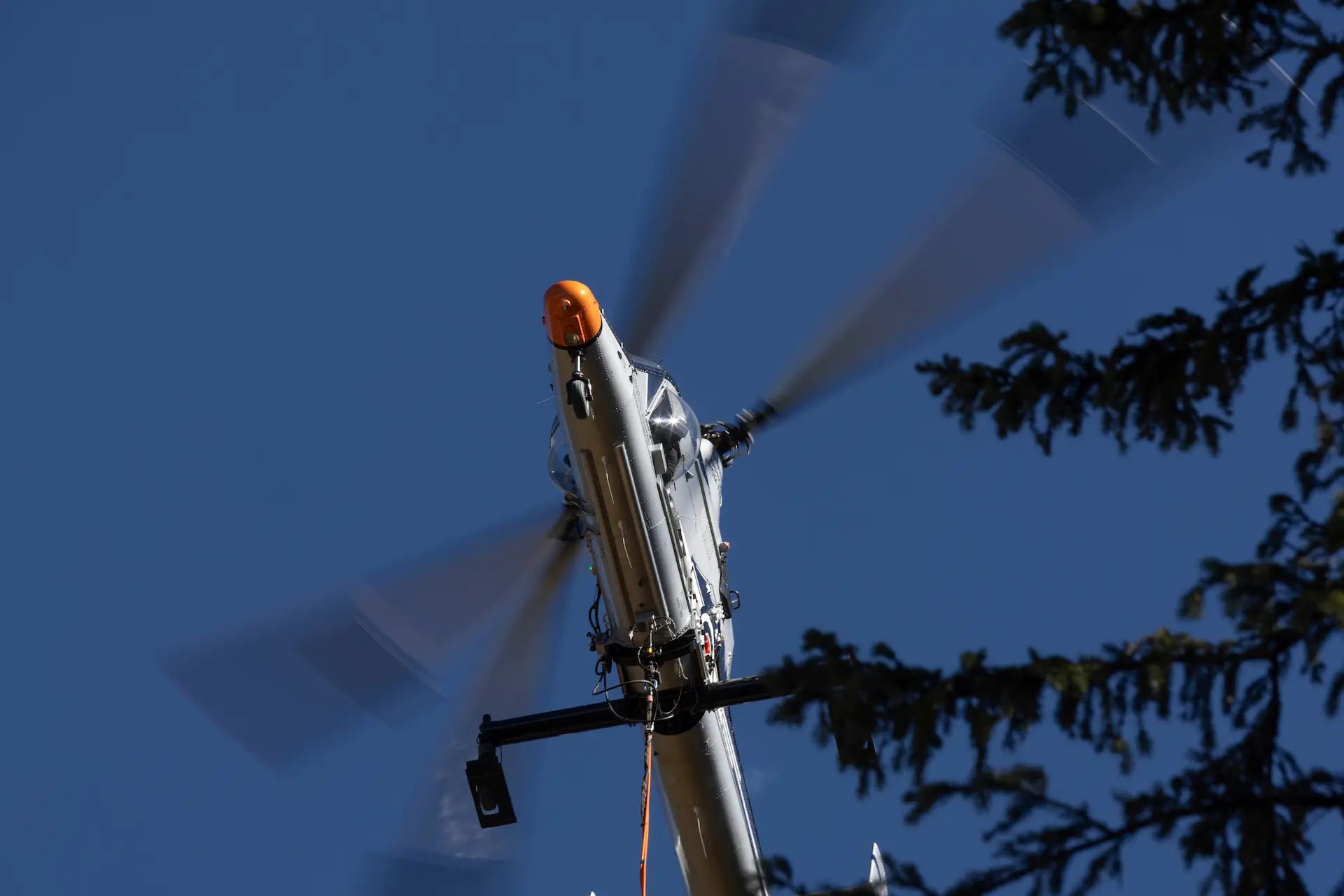
Gray is noncommittal about plans for the future, but remarked, “We’re pretty happy where we’re at but everything could change tomorrow of course, although that is not likely.” With regard to the fleet, he admits that the Enstrom is really more suited to sea-level operation and that it may be practical to replace it with a more altitude-capable machine – possibly such as an MD530F or similar. “I’d say we’re open to exploring new markets, but we will be picky about anything we look to go into. I really like being out in the field, being involved in the day-to-day operations and in customer relations, putting a face to it.” The Grays have clearly surrounded themselves with very talented, skilled, professional people such as Chief Pilot John Whedon who has been with MBR Helicopters for over nine years and flies both the K-Max as well as the AS350B3e and H125s. Asst Chief Pilot Shannon Bowman has also been with MBR for the nearly the same amount of time and is another who is regularly seen behind the controls of both helicopter types. “Both John and Shannon play a vital role in the day to day operations of MBR Helicopters” explained Bryson. “We’re always learning, so looking back now there are things that maybe we’d have done differently,” he admitted, but concluded, “We’ve always been improving though, so looking at the big picture, I’m really happy with where we’re at today.”
“We’re always thinking and continuing to explore here we head next, but it’s important to us not to overstretch. We have to look after our people because it’s about far more than just money.”